Chemical Properties
Fused Silica Chemical Composition
Translume works with Fused Silica (also called fused quartz). This glass is composed exclusively of high-purity silica (SiO2) in amorphous (non-crystalline) form. In contrast, other common glasses (Pyrex, borosilicate, soda-lime, etc.) are mixed composition glasses – in addition to SiO2, they include such ingredients as Na2O, CaO, and B2O3. These additional ingredients modify the optical and mechanical characteristics of the glass and lower the melt temperature of the mix. Fused Silica, on the other hand, is pure SiO2. It has a much higher working and melting temperature than other common optical glasses, and it also has exceptional optical, thermal, and mechanical properties.
Fused Silica Chemical Purity
Contaminants, despite their presence at very low levels, have subtle yet significant effects. Purity is mostly determined by the raw material, the manufacturing method, and subsequent handling procedures. Special precautions must be taken at all stages of the manufacturing process to maintain high purity.
The most common impurities are metals (Al, Na and Fe among others), water (present as OH groups), and chlorine. These contaminants affect the viscosity, optical absorption, and electrical properties of the glass.
Chemical Compatibility
Due to its pure composition, Fused Silica is an extremely inert glass. It is compatible with the vast majority of chemicals used in the industry and in the laboratory. There are only a few uncommon materials that will attack it, including HF (hydrofluoric acid) and hot KOH (Potassium hydroxide).
Thermal Properties
Coefficient of Thermal Expansion (CTE)
Fused Silica has a remarkably low coefficient of thermal expansion, which varies only slightly with temperature.
Fused Silica Mean Coefficient of Thermal Expansion (Source: Präzisions Glas & Optik GmbH, Menden, Germany):
- 0.52 x 10-6/K over the 5°C to 35°C temperature range
- 0.57 x 10-6/K over the 0°C to 200°C temperature range
- 0.48 x 10-6/K over the -100°C to 35°C temperature range
This material characteristic imparts fused silica a high resistance to thermal shock, and makes it an excellent material for applications that require the utmost in dimensional stability over a large temperature range. For comparison, INVAR (a nickel-iron alloy), which has the lowest thermal expansion among all metals and alloys near room temperature, has a mean coefficient of thermal expansion that is more than twice that of Fused Silica (1.3 x 10-6°/K over the 20°C to 100°C temperature range).
Thermal Conductivity
Fused Silica is an excellent thermal insulator. Its thermal conductivity is only 1.38W/mºK (measured at 25ºC), which is one of the lowest for any solid. For comparison, this value is 100-fold lower than that of silicon (148W/mºK @ 25 C); and one eighth of that of INVAR (10.5 W/mºK @ 25 C).
Optical Properties
Fused Silica offers a set of optical characteristics that compare favorably with other optical materials. It is transparent from the deep ultraviolet (UV) to the mid-infrared.
Optical Absorption
Fused Silica is transparent in the ultraviolet, visible, and near infrared.
Synthetic Fused Silica
Unless otherwise specified, we work with synthetic fused silica.
Shown here is a typical transmission for a 10-mm thick synthetic Fused Silica sample. The data is uncorrected for surface reflection (Fresnel) losses.
The absorption boundary on the ultraviolet side is deep in the UV. The exact location of the absorption edge is strongly affected by the presence of impurities. Synthetic Fused Silica, which is manufactured from an extremely pure precursor, offers the highest transparency in the UV of any glasses. On the infrared side, the source of intrinsic absorption is molecular vibration. The Si-O bond has a very strong absorption peak near 8.9 µm and at 4.5 µm (overtone frequency).
Additional absorption bands are present in the near infrared. These are caused by impurities. For example, water vapor creates absorption around 1.4, 2.1, and 2.8 µ m. Synthetic-grade Fused Silica is particularly likely to display water vapor absorption in the near infrared.
IR-Grade Fused Silica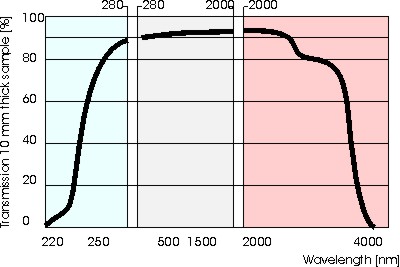
In Contrast IR grade fused silica contains a lot fewer water traces and shows significantly less absorption in the infrared. This material grade is, however, not as good in the UV.
Shown here is a typical transmission for a 10-mm thick IR-grade Fused Silica sample. The data is uncorrected for surface reflection (Fresnel) losses.
Index of Refraction of Fused Silica
(Source: www.mellesgriot.com)
Temperature Dependence of Refractive Index
The refractive indices of the glasses are not only dependent on wavelength, but also upon temperature. The dn/dT for Fused Silica is 1.1x10-5/ºC at 1064nm, near room temperature.
Electrical Properties
Fused Silica is an excellent electrical insulator
(All data- Source: Heraeus Quarzglas GmbH & Co, Kleinostheim, Germany):
Electrical Resistivity
- 1018 Ω*cm at 20 °C
- 1010 Ω*cm at 400 °C
Dielectric loss angle (tgδ)
- 5.0 x 10-4 @ 1 kHz
- 1.0 x 10-4 @ 1 MHz
- 4.0 x 10-4 @ 3 x 1010 Hz
Dielectric constant (ε)
- 3.70 from DC to 106 Hz (20 °C)
- 3.81 @ 3 x 1010 Hz (23 °C)
Mechanical Properties
Less known is the fact that Fused Silica has excellent elastic properties, making it a superior material for manufacturing micro-mechanical pieces that must flex to provide some type of motion. This is counter-intuitive: To the casual observer, glass is the personification of a breakable material, or what material scientists call a brittle material; and thus, one naturally assumes it can’t be used to manufacture flexible microdevices (MEMS). When using standard fabrication processes, such as ultrasonic drilling, lapping, or sand-blasting, this is indeed true. These processes create microscopic cracks, which lower the tensile strength of the glass and make it break easily. However, when silica glass is machined with our ultra-low stress femtoEtch™ process, microcrack formation is prevented, and the resulting part exhibits an exceptional elastic behavior.
For the skeptical readers, see the images above of a fused silica flexure being tested at Translume.
Density
Fused Silica is a light material. Its density is 2.202g/cm3 (To a very small degree, the density is influenced by the annealing conditions of the glass near the transformation temperature). By comparison, the density of the aluminum is approximately 2.6 g/cm3, and that of Invar is 8.1 g/cm3.
Elasticity Modulus
Fused Silica shows an almost perfect brittle-elastic behavior at temperatures lower than the transformation point. Fused Silica elasticity modulus is 73 GPa at 25ºC. By comparison, steel has a Young's Modulus of the order of 205 GPa.
Effect of Surface Flaws on Mechanical Properties
Fused Silica is extremely strong in compression, with a design compressive strength greater than 1.1 x 109 Pa. Under tension, the story is more complicated. Surface flaws - microcracks, scratches, indentations- can drastically reduce the inherent strength of any glass. As such, tensile properties are greatly influenced by these defects and by the manufacturing process that is used to create the desired Fused Silica object.
To date, the common practice has been to use a design tensile strength for Fused Silica with 'good' surface quality, taking into consideration both safety margin and fatigue, of 5 x 106 Pa. The Translume manufacturing process is exceptionally gentle and creates no microcracks. In fact some data indicate that our microfabrication process yield pieces stronger than raw fused silica.